Material Matters: A Technical Interview on Food-Safe Thermoforming Plastics
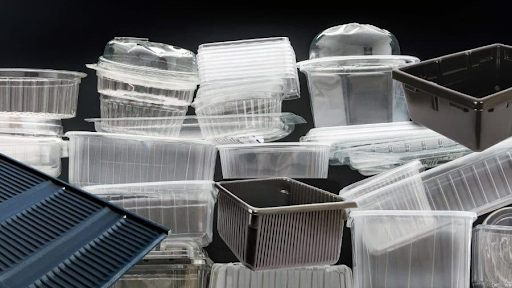
Micah Chaban is the Founder and Vice President of Sales at RapidMade, a digital manufacturing company specializing in advanced fabrication methods like 3D printing, CNC machining, and thermoforming. Known for their technical depth and material expertise, RapidMade works with engineers, designers, and procurement teams across industries—especially food and beverage—to optimize performance and compliance through smart material selection.
In this conversation, Micah offers insight into the thermoplastic materials RapidMade uses for food-grade thermoforming, explaining how performance factors like heat resistance, chemical stability, and cleanability influence both design and manufacturing decisions.
What are the top materials you use for food-safe thermoforming at RapidMade?
We primarily work with four plastics that consistently meet both performance and regulatory demands: High-Density Polyethylene (HDPE), Polypropylene (PP), High-Impact Polystyrene (HIPS), and Polyethylene Terephthalate Glycol (PETG). Each one has its place depending on what the customer needs. You’re balancing cost, durability, chemical compatibility, and hygiene protocols, and the right material will vary depending on the product’s environment and intended use.
Why is HDPE such a common choice for industrial food applications?
HDPE is a go-to because it’s extremely resistant to chemicals and moisture, and it handles physical abuse really well. It’s ideal for things like cutting boards, food processing surfaces, storage containers, and industrial bins. We recommend it where sanitation is critical and cleaning chemicals are aggressive. That said, it doesn’t like heat. It’ll warp in high-temperature environments, so if you need something that can go through a dishwasher or steam sterilization, HDPE isn’t the answer.
Where does Polypropylene fit in?
Polypropylene is your best option when you need a plastic that’s safe for repeated heat exposure. It handles boiling water, autoclaving, and microwave use without breaking down. That’s a huge advantage in foodservice environments where sterilization is routine. It also has great chemical resistance, like HDPE, but adds more flexibility and fatigue strength. We often use it in things like microwaveable trays, yogurt cups, beverage caps, and containers with living hinges.
Thermoforming PP is a bit more demanding—its higher melting point means tighter temperature control. But the tradeoff is performance. If the part is going to be cleaned with heat or needs to flex repeatedly, PP is probably your material.
How about HIPS? It’s widely used in food packaging.
Yes, High-Impact Polystyrene is everywhere in single-use packaging. It’s incredibly easy to thermoform, very affordable, and ideal for high-volume disposable items. We use it for takeout trays, bakery lids, and printed packaging.
The downside is durability. It has poor chemical and heat resistance, and it’s not especially impact-tolerant. We never recommend it for reuse or sterilization. It’s perfect for low-cost, short-life-cycle products that need to look good but don’t need to last.
PETG is known for its clarity—where does it stand in food-safe design?
PETG is an excellent choice when visual clarity is important. It’s clear, stiff, and impact-resistant, which makes it a favorite for clamshell packaging, beverage bottles, and any product that needs to show off its contents. But it does have limits. PETG scratches easily and doesn’t tolerate harsh cleaners or high heat. It’s not dishwasher-safe or autoclave-compatible.
It forms really well and keeps tight details, which makes it great for high-end packaging. But it needs to be treated carefully in cleaning and sanitation environments. For premium consumer-facing packaging, it’s hard to beat.
How do these materials differ in terms of cleaning and sterilization?
That’s where selection gets critical. HDPE and PP both handle chemical sanitation well. You can clean them with industrial-strength detergents, disinfectants, or degreasers. PP goes a step further—it’s the only one that can reliably survive autoclaving and other high-temperature cleaning protocols.
PETG and HIPS, on the other hand, don’t do well under thermal or chemical stress. PETG needs gentle, non-abrasive cleaners. HIPS should only be used with mild soap and water. They’re not built for rigorous sanitation.
Gamma sterilization is another option. HDPE, PP, and PETG can tolerate it, though you’ll see some material aging over time. HIPS usually becomes brittle when exposed to radiation.
What do you consider when recommending a material to a client?
First we look at the environment—what kind of stress the part will be under, how it’s cleaned, whether it’s single-use or reusable. Then we consider mechanical needs: Does it need to flex? Is it load-bearing? Does it need to be clear or printable?
Cost always plays a role, too. HIPS is the least expensive and easiest to form, so it’s ideal for disposable items. PETG costs more but looks fantastic. HDPE and PP are mid-range, but give you real durability and sanitation resistance.
It’s all about application fit. You can’t pick a material in isolation—you have to match it to how the part will actually function in the field.
Final thoughts for engineers or buyers making material decisions?
Know your cleaning process and performance needs up front. That’s what usually dictates the choice. It’s tempting to pick a material based on ease of forming or price, but if it can’t hold up to cleaning or the actual working environment, it’s going to fail. That’s where we come in—to help balance performance, cost, and compliance before anything goes to production.
For expert guidance on food-grade materials and custom thermoforming, reach out to RapidMade at rapidmade.com or email info@rapidmade.com to start a conversation.